What Are the Safety Considerations When Using a Welding Hose
Safety during welding operations is of the utmost significance since welding is an essential technique in many different sectors. While welding involves numerous safety measures, one crucial step that is sometimes missed is the appropriate handling and use of welding hoses. Welding hoses are essential for supplying the gases and fluids required for welding procedures, therefore ignoring safety precautions might result in dangerous circumstances. The primary safety factors to take into account while utilizing a welding hose will be discussed in this article.
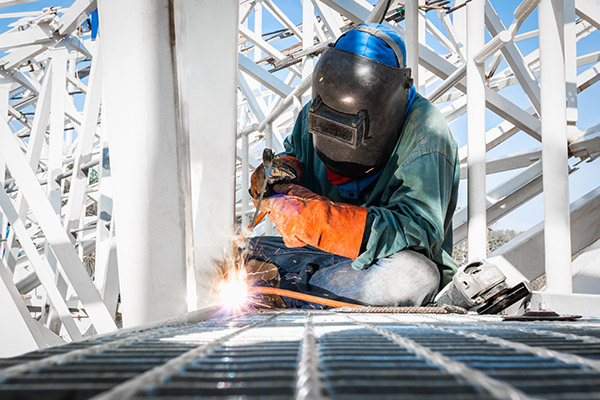
Hose Quality and Inspection
Investing in high-quality hoses from recognized welding hose manufacturers is the first step in guaranteeing safety while using welding hoses. Accident risk will be lower since a strong, well-made hose will be more resistant to wear, leaks, and damage. The hoses must be inspected often to look for wear, cracks, or leaks. To avoid any risks, any broken hoses should be replaced right away.
Proper Storage and Handling
Welding hoses need to be kept clean, dry, and out of chemicals, bright sunlight, and other conditions that might weaken the components. To avoid kinks, twists, or tangles that might jeopardize the integrity of the hose, proper coiling and storing procedures should be used. Carefully handling the hoses and avoiding dragging or treading on them will extend their life and keep them safe.
Correct Hose Connections
To avoid leaks and guarantee the delivery of gases and fluids at the correct pressure, proper hose couplings are essential. Make that the hoses and welding equipment are connected securely and without leaks. For a secure connection, it is crucial to utilize the fittings, clamps, and regulators that the welding hose manufacturers prescribe.
Adequate Hose Length
The key safety factor is choosing the appropriate hose length. A hose that is too long might provide a tripping risk and result in accidents. A hose that is excessively short, on the other hand, could hinder motion and put stress on the hose connections. To guarantee both safety and efficiency during welding operations, evaluate the work area and choose a suitable hose length.
Proper Hose Positioning
To reduce the chance of damage or interference, welding hose placement should be properly thought out. Hoses should not be placed next to edges with sharp edges, hot surfaces, or busy places. To avoid tripping or inadvertent damage, secure the hoses with appropriate protective coverings or barriers if they must traverse walkways or other work areas.
Protection Against Heat and Flames
During welding procedures, welding hoses are exposed to very high temperatures and flames. To avoid mishaps and hose damage, the hoses must be shielded from heat and sparks. In order to protect the hoses and keep them away from possible ignition sources, think about using heat-resistant coverings, sleeves, or fire blankets.
Always put safety first while welding, and for help choosing and utilizing the proper hoses for your particular applications, speak with
welding hose manufacturers.
Conclusion
To avoid mishaps, injuries, and equipment damage, it's essential to practice safety while utilizing a welding hose. Maintaining a safe welding environment also depends on having the right hose connections, length, and location. Finally, shielding hoses from heat and flames reduces the likelihood of accidents. Welders may improve their own safety and the effectiveness of welding operations by following these safety precautions.